Recycling technology specialist Sutco has announced the findings of research into an automated bunker management system for packaging waste sorting plants.
The development and implementation work is part of a research project backed by Germany’s Ministry of Economic Affairs and Energy.
In a statement announcing what it sees as the success of the project, Sutco explains that the new system increases the level of automation and overall efficiency of sorting facilities – typically a ‘materials recycling facility’ in the UK.
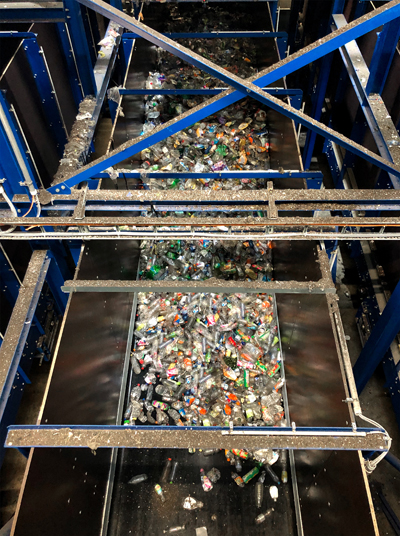
The Sutco bunker management system monitors the flow of material into bunkers for automatic emptying and baling
The plants which have seen use of the new bunker management system, explained the company, handle packaging waste of all kinds such as PP, PET, HDPE and LDPE alongside paper, TetraPaks and aluminium cans with these all needing to be cleanly separated from each other and collected in bunkers at the end of the sorting process.
The goal of the project was to increase the overall efficiency of the sorting process up to its final stage, the compression of the secondary raw materials produced from the recycling stream into bales.
Packaging
Sutco noted that a sorting plant for packaging has on average over 10 to 20 bunkers for storing the sorted materials. It explains that the bunkers fill up at varying rates, depending on the material. Some with bulky materials are likely to have to be emptied up to five times an hour, while the aluminium bunker may only need emptying once a day.
The company states: “Previously, once a bunker was full, the press operator would have to withdraw the contents manually and transfer it via a conveyor belt to the press. In our research project, Sutco developed automated bunker management, determining the perfect time to empty the bunker using fill level measurements.
“The system only empties the individual bunkers when they contain a volume suitable for one, two or three bales. During manual operation, the press operator cannot keep an overview at all times of the filling speeds of all the bunkers, empty them at exactly the right moment and also consider the activity status of the corresponding bale press in each case. Not until the introduction of the specially designed software by Sutco, using a mathematical model to process recorded data and measurements by the millisecond, could this complex process be optimised.”
‘Less space’
One advantage of the bunker management system for new plants is that much less space is needed for the bunkers – Sutco estimates that a standard buffer reserve capacity of up to 60% of bunker volume is no longer required (e.g. for aluminium).
In the research work, Sutco said that the greatest challenge was the flexible design of material-dependent self-adjusting programs. “For each material, an automatic comparison of the bale length and bunker fill level is constantly carried out. In this way, Sutco bunker management not only ensures the guaranteed production of desired bale qualities, but also independently optimises its own processes, constantly increasing its precision.”
The processing status of the baler is coupled to the fill level of the bunker in question. “The program takes account of the different fill levels of the bunkers and, where these are the same, gives priority to the bunker that will fill quickest.”
Sutco Recyclingtechnik is based in Bergisch Gladbach, Germany.
The post Sutco automates bunker management for MRFs appeared first on letsrecycle.com.
Source: letsrecycle.com Plastic