Following the recent webinar on letsrecycle.com, Morgan Lynch, Global Head of Digital Engagement for AMCS, looks at some of the common challenges in managing a network of sub-contractors and the latest solutions designed to tackle these head on.
The digitisation of the waste and recycling sector is continuing at pace, and bringing about significant technological change with it, ranging from route optimisation to driverless vehicles and the application of Artificial Intelligence.
In contrast to previous ‘leaps’ in technology, which have resulted in man and machine complementing each other, we are now starting to see the automation of a number of cognitive tasks. This will make humans and software-driven machines substitutes, rather than compliments. Whilst some of these technologies may never cross over into the waste and recycling sector, and some won’t be commonplace for a number of years, there are areas where operators can already benefit from these advancements, such as with subcontractor management.
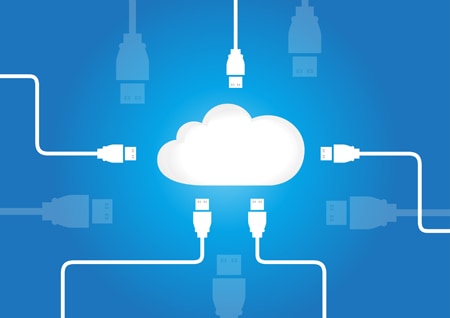
Using the cloud can be of benefit in managing subcontractors (picture: shutterstock)
Subcontracting
Whether it’s the basis of your business, or forms part of a customer service or growth strategy, subcontracting work is an integral part of delivering waste and recycling services in the UK. Subcontracting however, does not come without its challenges. This starts with identifying which supplier to use.
Selection of subcontractors and deciding who is likely to provide the right service at the right price has always involved a degree of ‘gut feel’. It is also heavily based on relationships, with certain contractors becoming the default choice in a particular area or for a particular service. This situation is completely understandable given the immediate pressure is to service the customer. It is not always practical to go out to the market and understand the pricing and services that are available, but undoubtedly it can lead to bad decisions being made.
Platform
The recent fast-paced expansion of Cloud-based computing has enabled us to make some significant improvements in the way we interact and manage subcontractors. The Cloud has provided a platform for real-time data and given us the ability to share it across the business and with selected partners. It has also dramatically reduced the need to use paper, emails or calls to share data and now means that every operation or employee can act as a data collection channel. These numerous data sources can then be used to make better decisions, improve processes and develop a new model that we call ‘connected subcontracting’. This helps us remove the need for un-auditable decisions based on ‘gut feel’ or out-of-date information, and enables us to learn from previous experiences.
To enable the implementation of connected subcontracting there are three core pieces of technology that need to be in place:
The Supplier Network – connected subcontracting treats suppliers as a single dynamic framework. Links are then formed between primary operator and subcontractors with attributes such as ‘trust levels’ applied to each. This supports the rapid exchange of data and allows us to build-in modern due diligence practices. It also facilitates zero touch procurement, with no human interaction required from assigning the work through to its invoicing.
The Marketplace – This enables the creation of a free market that increases competition and drives greater efficiency for all parties. As decision-making is data-driven and the due diligence is already existing within the system, the speed of transactions can significantly increase. An example might be the implementation of a fully-automated reverse auction for new work. Here the supplier bidding the lowest price (at the defined level of quality), wins the business and automatically has the work assigned to them.
Enterprise Social Network – In practice, this involves setting up a supplier contact centre to manage any exceptions and complex problems that will still require human interaction. A communications platform is built within the data-driven framework to allow structured and auditable problem solving, in an environment that enables learning and improves streamlining. This approach will, in time, reduce the amount of jobs requiring intervention and increase productivity.
Once these building blocks are in place, businesses can then set up a connected subcontracting system which operates in real time; requires no human interaction from job allocation to invoicing; is based upon data driven decisions and is de-risked by the due diligence that is embedded in the system. This efficient allocation and completion of work enables businesses to do more with less resources and create a platform that will ultimately be more profitable and support their future growth.
Related links
AMCS Group
The post Managing subcontractors well appeared first on letsrecycle.com.
Source: letsrecycle.com Waste Managment