Amey’s gasification plant in Milton Keynes is up and running, and despite some teething problems, it is now operating at expected levels of energy generation.
The advanced thermal treatment (ATT) plant is one of three technologies at the firm’s Milton Keynes Waste Recovery Park (MKWRP), sited in Old Wolverton, along with a mechanical treatment system and dry anaerobic digestion (AD) plant.
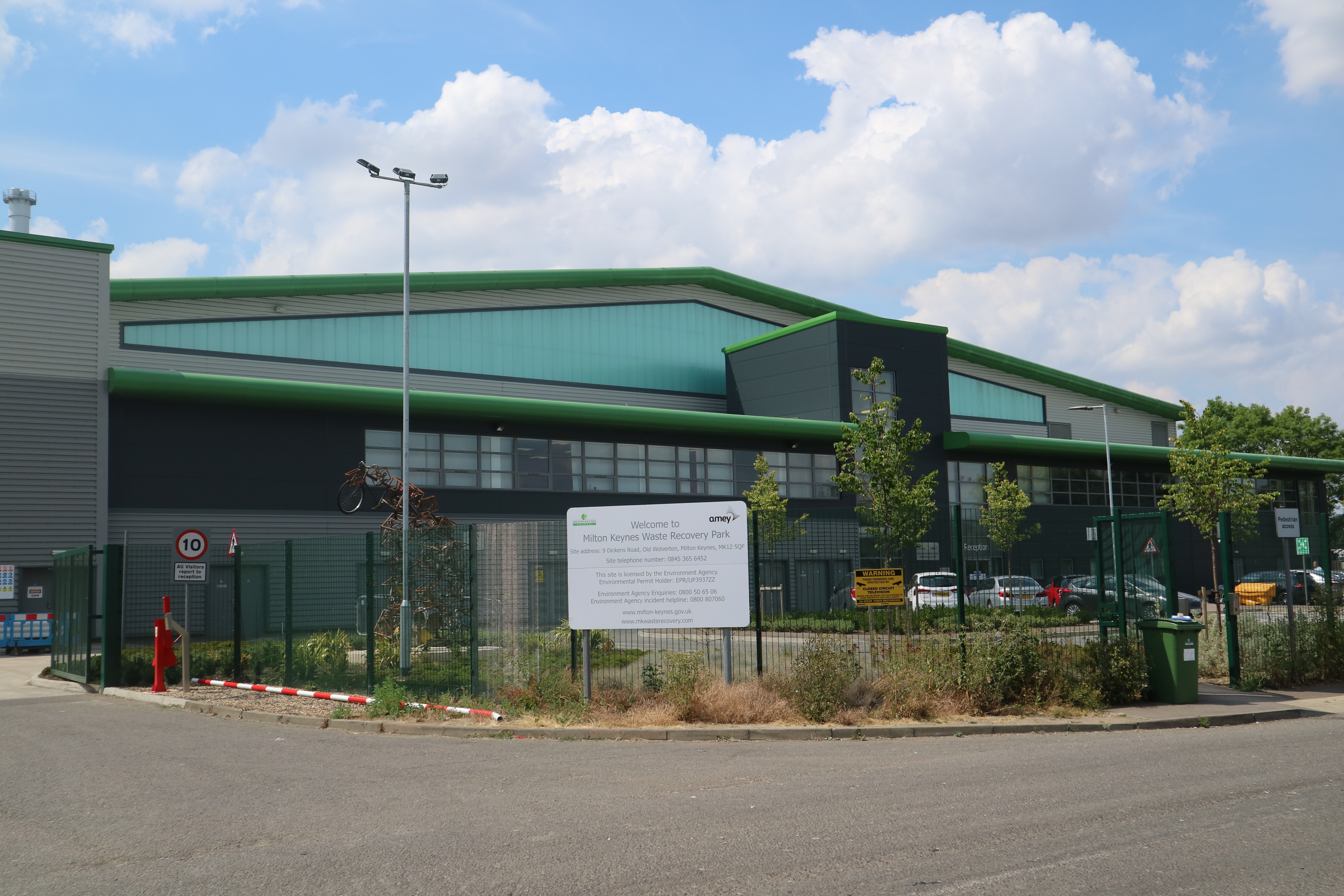
Milton Keynes Waste Recovery Park was developed under a 15-year contract between Amey and Milton Keynes council
MKWRP was developed under a 15-year contract between environmental services firm Amey and Milton Keynes council which was signed in 2013. The contract sees Amey taking in municipal refuse from households and other sources in the borough.
The facility, which became fully operational in March this year, has capacity to treat 132,000 tonnes per year of ‘black sack’ waste.
Gasification
Amey stepped in itself to ensure completion of the ATT facility following the demise of contractor Energos – which was supplying the technology. Energos went into liquidation in 2016 (see letsrecycle.com story), near the end of the build, but Amey were able to complete the construction with the technology.
This caused a number of difficulties with completing the ATT plant, which was expected to be fully operational in in autumn 2016. However, the mechanical treatment facility and anaerobic digestion plant were commissioned on schedule.
Despite the setback on the ATT, Jon Callaghan, Amey’s business director, seems pleased with the way the gasification plant is operating.
“The gasifier is operating in line with its design capacity and is now proving to be a really efficient technology,” he says.
And, it has become the first gasification plant in the UK to become fully operational, with plants including Suez’ in Surrey (see letsrecycle.com story), and Hoddesdon (see letsrecycle.com story) running behind schedule.
However, Peter Waller, account director, MKWRP, Amey, explains that it’s “not unusual” for projects such as these to be delayed when gasification is still considered a relatively new technology in the waste sector.
Gasification has been around since the later nineteenth century for coal gas production, he says, but for the UK market the treatment of waste is relatively new.
Technologies
Where the company feels the site is unique is the combining of three technologies at one site.
- The mechanical treatment and separation technology, provided by Stadler, processes around 140,000 tonnes per annum of residual waste and extracts 32,000 tonnes of organic waste.
- The anaerobic digestion plant then processes the 32,000 tonnes of organic waste generating around 1MWe and a compost-like output (CLO).
- Finally, the EfW gasification plant processes up to 94,000 tonnes per annum generating around 6MWe.
“What this site offers is that flexibility and continually trying to capture materials that ordinarily would have been lost through a more traditional type of treatment facility.”
Jon Callaghan
Amey
“What this site offers is that flexibility and continually trying to capture materials that ordinarily would have been lost through a more traditional type of treatment facility,” explains Jon Callaghan.
And, one of the reasons for the efficiency of the gasification plant is the steady flow of material, Mr Waller reveals.
“We have a reasonably consistent feedstock,” he says. “The MT prepares a feedstock and we mix it in the bunker.”
This is due to having the front end mechanical recovery technology which allows infeed material to be controlled and gives the ability to mix material before entering the ATT, explains Mr Callaghan.
The facility takes around 50% of its material from Milton Keynes Council. Remaining feedstock comes from other local authorities, including Central Beds, along with local commercial customers.
So far, the facility has processed over 100,000 tonnes of material, Mr Waller explains, and it is diverting around 95% of material away from landfill. In total, around 9% of the material is recovered as recyclate.
Dry AD
Dry AD is a technology commonly seen throughout Europe, however, there are few plants utilising the process here in the UK.
According to Mr Waller, there are only three facilities in the UK using the same technology as the Milton Keynes plant – which comprises of nine fermenters – and around two or three other using dry technologies.
The dry AD process lends itself to municipal black bag waste, explains Mr Waller, because it is “far more robust” and can deal with the levels of contamination more effectively.
However, heavy metals found in black bag waste can kill the bugs needed to break down the organics in the anaerobic digester, Mr Waller says.
“Flexibility is particularly important for Milton Keynes hence there’s two lines of thermal treatment and nine fermenters so that if one does go down and we kill the bugs in one fermenter we’ve got eight others,” adds David Proctor, waste management services client manager, Milton Keynes council.
[gallery_placement]
“It needs to be wet and pumpable in wet AD hence it lends itself to food waste and agricultural crops; whereas black bag has a good chance of having everything in it so it’s not really pumpable.”
Future
The company and the council believe the facility has been a good decision for the future. “There’s quite a bit of talk at the moment about incineration bans and taxes […] if they want to bring in a tax for burning plastics or metals we’ve already taken that out,” Mr Proctor concludes.
For Milton Keynes, the development of the project epitomises the spirit of the council in leading the field in terms of new projects. Milton Keynes was one of the first authorities in the UK to develop a materials recycling facility in the early 1990s close to the site of the new gasification plant.
The post Amey overcomes ‘teething problems’ in Milton Keynes appeared first on letsrecycle.com.
Source: letsrecycle.com Waste Managment