With news on: Rabbit selects Ajax; Liberty House invests in material handler; LKM takes delivery of car baler; LondonEnergy invests in JCB; and, UNTHA shredders aid paper production.
Rabbit selects Ajax twin screw feeder
Solids handling specialist, Ajax Equipment, has supplied construction and commercial waste firm, Rabbit Waste Management, with a twin screw feeder, horizontal collecting conveyor and two screw feeders to handle fines from a waste stream and sawdust.
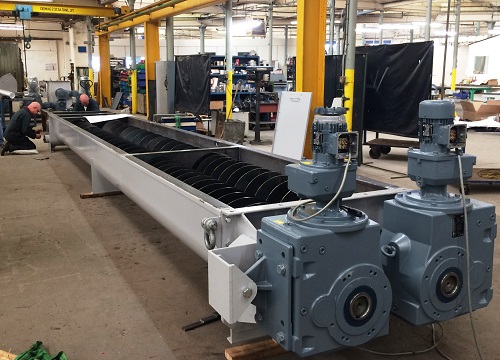
Ajax Equipment has supplied Rabbit Waste Management with a twin screw feeder, horizontal collecting conveyor and two screw feeders
Once collected, Rabbit sorts waste removing all recyclable materials for reuse with non-recyclable biomass being used as fuel in company’s waste-to-energy facility.
Ajax’s twin screw feeder supplies the combustion system via a chain and disk conveyor and two feeders. Constructed in mild steel, the twin screw feeder collects the fines and sawdust from a hopper, transferring the materials to the collecting conveyor.
“The original screw feeder provided by a different supplier was very problematic meaning our system was unusable. Ajax undertook tests on the material and came up with their recommended design, which they supplied; this is working very effectively,” said Mick Adams, managing director, Rabbit Waste Management.
Liberty House invests in Liebherr material handler
Producers of speciality steels, Liberty House Group, reports to be “gearing up” for an upshift in scale, as it looks to process over 500,000 tonnes of incoming recyclable material at its Rotherham plant in the coming months.
To cope with operations, Liberty House selected a Liebherr LH 120 gantry-mounted material handler to add to its material handling fleet.
Liberty House Group reports to be one of the largest producers of speciality steels in the country with plants in England, Scotland and Wales. Speciality Steels, based in South Yorkshire, is one of their more recent acquisitions, and supplies speciality steels worldwide, suitable for use in the aerospace, engineering and automotive industries.
The material handler has been purchased with a comprehensive service arrangement from the manufacturer.
LKM takes delivery of car baler
Waste management firm, LKM Recycling in Sittingbourne, has taken delivery of a Predator car baler.
LKM Recycling will be using the baler to increase its end of life vehicle output capacity. The firm said it will speed up the turnaround to supply customers, as well as offering tighter compaction and varying shapes such as logs and flat pressed shells.
The tight compaction means safer storage in yards, more stable loading on vehicles that maximises the load capacity, LKM said. According to the company, the Predator can bale 2 cars in less than 1 minute.
Commenting on the investment, Ryan Eastwood managing director of LKM Recycling said: “We are really pleased to get the new baler commissioned. This gives both us and our customers some real benefits in terms of efficiencies, speed of turnaround and choice.”
LondonEnergy invests in JCB machinery
Waste management firm, LondonEnergy Limited, has invested almost £400,000 in four JCB 5CXs.
They have been delivered to recycling centres in North London, which LondonEnergy operates on behalf of the North London Waste Authority.
According to LondonEnergy, the JCB 5CX model will provide operators with “much greater flexibility” than their existing mobile plant which were incurring high maintenance and repair costs. The 7.10 metre excavator arm with the multi-purpose jaw bucket will allow bins to be compacted efficiently. The integrated stabiliser legs can raise the machine by up to 400mm to provide “excellent visibility and reach into bins,” the company said.
The JCB 5CXs also come fitted with safety benefits which include: a protective rear screen to shield the operator from flying debris, a door safety alarm which alerts the operator if the door is opened in the raised position and seat belt alarms.
UNTHA XR shredders aid recycled paper production
Two UNTHA XR waste shredders are now in operation for VPK Packaging Group in continental Europe, shredding pulped ropes as part of a “closed loop” paper production process.
Manufacturing 900,000 tonnes of paper per year from 100% recycled materials, VPK said its mill in Dendermonde, Belgium and Blue Paper Mill, co-owned with Klingele Papierwerke, in Strasbourg, France, generate a waste by-product including “complex” pulper ropes.
This multifaceted 1:3 metal and plastic material was previously treated off site by a third party, the company said. However, the new shredding investment means that both sites can now process the waste themselves to manufacture an alternative fuel for their own energy generation.
At Dendermonde, untreated pulper rope waste is being fed into an UNTHA XR3000C shredder via a ceiling-mounted claw grab, at a throughput rate of five tonnes per hour. A 50mm screen ensures homogenous particle sizing before the fraction drops onto a horizontal discharge conveyor. The shredded material then passes up an elevated conveyor to an electro-magnetic FE-separator, where metals are extracted for onward sale and recycling. The finished product is an SRF specification fuel that VPK uses in its own on-site Waste to Energy facility.
The post Equipment news round-up (31/07/2018) appeared first on letsrecycle.com.
Source: letsrecycle.com General